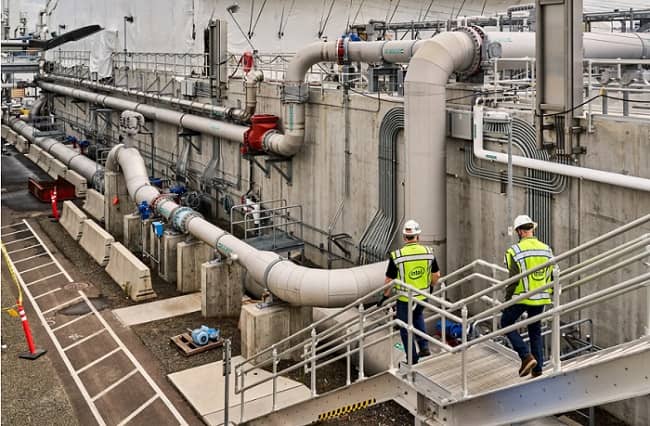
Algunos cuentan con más de 50.000 millones de diminutos transistores que son 10.000 veces más pequeños que el grueso de un cabello humano. Se elaboran en fábricas gigantescas y extremadamente limpias que pueden tener siete pisos y la longitud de cuatro campos de fútbol americano.
Los microchips son, en muchos sentidos, el elemento vital de la economía moderna. Hacen funcionar computadoras, teléfonos inteligentes, automóviles, electrodomésticos y muchos otros dispositivos electrónicos. Pero la demanda mundial por ellos ha aumentado desde la pandemia, la cual también provocó interrupciones en la cadena de suministro, lo que generó una escasez mundial.
Eso, a su vez, está fomentando la inflación y activando las alarmas de que Estados Unidos se está volviendo demasiado dependiente de los chips fabricados en el extranjero. El país representa solo alrededor del 12 por ciento de la capacidad mundial de fabricación de semiconductores; más del 90 por ciento de los chips más avanzados provienen de Taiwán.
Intel, un titán de Silicon Valley que busca restaurar su antiguo liderazgo en la tecnología de fabricación de chips, está haciendo una apuesta de 20.000 millones de dólares para aliviar el déficit de chips. Está construyendo dos plantas en su complejo de fabricación de chips en Chandler, Arizona, que tardarán tres años en completarse, y hace poco anunció planes para una expansión potencialmente mayor, con nuevas sedes en New Albany, Ohio y Magdeburgo, Alemania.
¿Por qué fabricar millones de estos componentes diminutos se traduce en construir —y gastar— tanto? Un vistazo al interior de las plantas de producción de Intel en Chandler e Hillsboro, Oregón, ofrece algunas respuestas.
¿Qué hacen los chips?
Los chips, o circuitos integrados, comenzaron a remplazar a los voluminosos transistores individuales a finales de la década de 1950. Muchos de esos pequeños componentes se producen en una pieza de silicio y se conectan para trabajar en conjunto. Los chips resultantes almacenan datos, amplifican señales de radio y realizan otras operaciones; Intel es famosa por una variedad llamada microprocesadores, que realizan la mayoría de las funciones de cálculo de una computadora.
Intel ha logrado reducir los transistores de sus microprocesadores a tamaños alucinantes. Pero su rival, Taiwan Semiconductor Manufacturing Co. (TSMC), puede fabricar componentes aún más pequeños, una razón clave por la que Apple la eligió para fabricar los chips para sus iPhones más recientes.
Tales victorias de una empresa con sede en Taiwán, una isla que China reclama como propia, se suman a las señales de una creciente brecha tecnológica que podría poner en riesgo los avances en computación, dispositivos de consumo y hardware militar, tanto por las ambiciones de China como por las amenazas naturales en Taiwán, como terremotos y sequías. Además, ha puesto de relieve los esfuerzos de Intel por recuperar el liderazgo tecnológico.
¿Cómo se hacen los chips?
Los fabricantes de chips están colocando más y más transistores en cada pieza de silicio, lo cual explica por qué la tecnología logra hacer más cada año. También es la razón por la que las nuevas fábricas de chips cuestan miles de millones de dólares y menos compañías tienen el dinero para construirlas.
Además de pagar los edificios y la maquinaria, las empresas deben invertir mucho en el desarrollo de los complejos pasos de procesamiento utilizados para elaborar chips a partir de obleas o láminas de silicio del tamaño de una placa. A este tipo de fábricas se les llama fabs.
Enormes máquinas proyectan diseños para chips en cada oblea y luego depositan y graban capas de materiales para crear sus transistores y conectarlos. Hasta 25 obleas se pueden mover a la vez entre esos sistemas, en cápsulas especiales dispuestas en pistas automatizadas que cuelgan.
Procesar una oblea conlleva miles de pasos y hasta dos meses. TSMC ha marcado el ritmo de la producción en los últimos años, al operar gigafabs, instalaciones con cuatro o más líneas de producción. Dan Hutcheson, vicepresidente de la firma de investigación de mercado TechInsights, estimó que cada sitio puede procesar más de 100.000 obleas al mes. También calculó la capacidad de las dos instalaciones que Intel tiene previsto construir por 10.000 millones de dólares en Arizona en aproximadamente 40.000 obleas mensuales cada una.
¿Cómo se empaquetan los chips?
Después del procesamiento, la oblea se corta en chips individuales. Estos se prueban y se envuelven en paquetes de plástico para conectarlos a placas de circuitos o partes de un sistema.
Ese paso en particular se ha convertido en un nuevo campo de batalla, porque es más difícil hacer transistores aún más pequeños. En la actualidad, las empresas están apilando múltiples chips o colocándolos uno al lado de otro en un paquete, conectándolos para que actúen como una sola pieza de silicio.
En una realidad donde empaquetar un puñado de chips juntos ya es rutina, Intel ha desarrollado un producto avanzado que utiliza una nueva tecnología para agrupar una cantidad notable de 47 chips individuales, entre ellos algunos fabricados por TSMC y otras compañías, así como los producidos en las fábricas de Intel.
¿Qué hace que las fábricas de chips sean diferentes?
Los chips de Intel en general se venden por cientos o miles de dólares cada uno. Por ejemplo, en marzo, Intel lanzó su microprocesador más rápido para computadoras de escritorio a un precio inicial de 739 dólares. Una mota de polvo invisible al ojo humano puede dañar uno de estos microprocesadores. Es por eso que las fabs deben ser más limpias que el quirófano de un hospital y requieren de sistemas complejos para filtrar el aire y regular la temperatura y la humedad.
Estas fábricas también deben ser inmunes a casi cualquier vibración, que puede provocar averías de equipos costosos. Es por eso que las salas limpias de las fabs, también llamadas de ambiente controlado o sala limpias, se construyen sobre enormes bloques de concreto encima de amortiguadores especiales.
También es crucial la capacidad de mover grandes cantidades de líquidos y gases. El nivel superior de las fábricas de Intel, que tienen unos 21 metros de altura, tiene ventiladores gigantes para hacer circular el aire hacia la sala limpia que está directamente debajo. Debajo de la sala limpia hay miles de bombas, transformadores, gabinetes eléctricos, tuberías y enfriadores que se conectan a las máquinas de producción.
La necesidad de agua
Las fabs son operaciones que requieren mucha agua. El agua es necesaria para limpiar las obleas en muchas etapas del proceso de producción.
Las dos instalaciones de Intel en Chandler extraen de forma colectiva alrededor de 42 millones de litros de agua al día de la empresa local de servicios públicos. La futura expansión de Intel requerirá mucho más, lo que parecer ser un desafío en un estado asolado por la sequía como Arizona, que ha recortado las asignaciones de agua a los agricultores. Sin embargo, la agricultura en realidad consume mucha más agua que una planta de chips.
Intel afirma que sus locaciones en Chandler, que dependen del suministro de tres ríos y un sistema de pozos, recuperan alrededor del 82 por ciento del agua dulce a través de sistemas de filtración, estanques de sedimentación y otros procesos. Esa agua es devuelta a la ciudad, la cual opera instalaciones de tratamiento financiadas por Intel y que la redistribuye para riego y otros usos no potables.
Intel espera ayudar a impulsar el suministro de agua en Arizona y otros estados para 2030, a través de la colaboración con grupos ambientalistas y otros en proyectos que ahorran y restauran agua para las comunidades locales.
¿Cómo se construyen las “fabs”?
Para construir sus futuras fábricas, Intel necesitará cerca de 5000 trabajadores de obras calificados durante tres años.
Tienen mucho por hacer. Se espera que la excavación de los cimientos elimine 680.450 metros cúbicos de tierra, que serán transportados a un ritmo de un camión de volteo por minuto, dijo Dan Doron, jefe de construcción de Intel.
La compañía espera verter más de 340.226 metros cúbicos de concreto y usar 100.000 toneladas de acero de refuerzo para los cimientos, una cantidad mayor que en la construcción del edificio más alto del mundo, el Burj Khalifa en Dubái, Emiratos Árabes Unidos.
Algunas grúas para la construcción son tan grandes que se necesitan más de 100 camiones para transportar las piezas para ensamblarlas, informó Doron. Las grúas levantarán, entre otras cosas, enfriadores de 55 toneladas para las nuevas fabs.
Patrick Gelsinger, quien se convirtió en el director ejecutivo de Intel hace un año, está presionando al Congreso estadounidense para que otorgue subvenciones para la construcción de fabs y créditos fiscales para la inversión de equipos. Para administrar el riesgo de gasto de Intel, Gelsinger planea enfatizar la construcción de “carcasas de fabricación” que pueden dotarse con equipos para responder a los cambios del mercado.
Para afrontar la escasez de chips, Gelsinger tendrá que cumplir con su plan de producir chips diseñados por otras compañías. Sin embargo, una sola empresa no puede hacer mucho; productos como teléfonos y automóviles requieren componentes de muchos proveedores, así como chips más antiguos. Además, ningún país puede por sí solo fabricar semiconductores. Aunque impulsar la fabricación nacional puede reducir de cierta manera los riesgos de suministro, la industria de los chips seguirá dependiendo de una compleja red mundial de empresas para obtener materias primas, equipos de producción, software de diseño, talento y fabricación especializada.